Table of Contents
Introduction
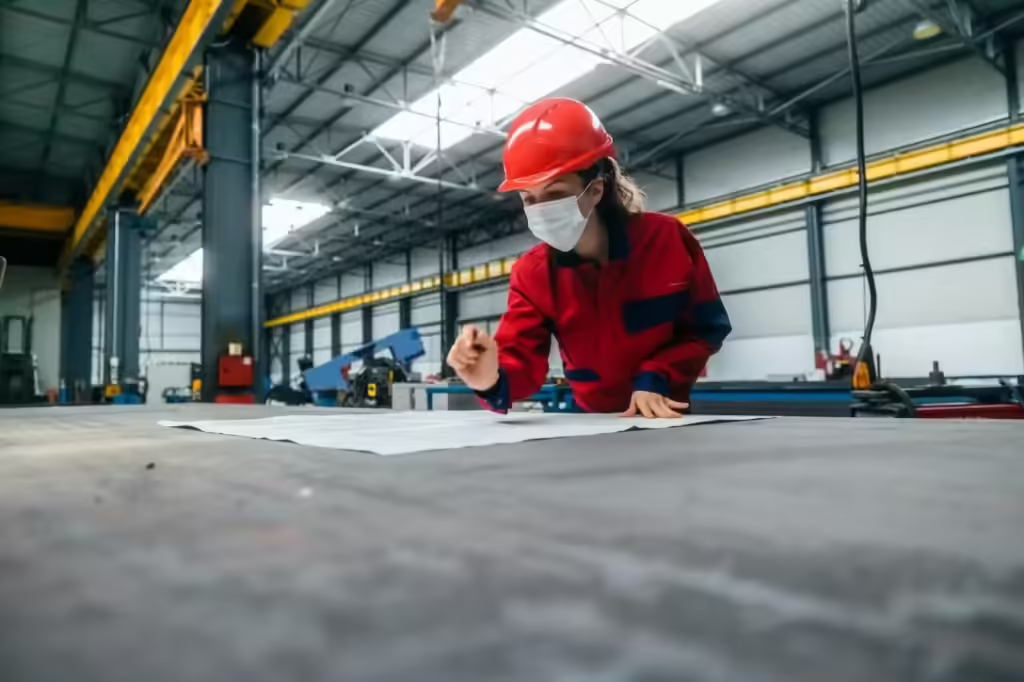
Hydraulic hose crimp fittings are essential components in fluid power systems, widely used in industries such as construction, manufacturing, agriculture, and transportation. These fittings provide leak-proof connections between hoses and hydraulic machinery, ensuring safe and efficient power transmission. However, despite their significance, issues with hydraulic hose crimp fittings are not uncommon. Problems can arise due to improper installation, material mismatch, or operational wear.
Understanding and resolving these problems is key to maintaining a reliable and high-performance hydraulic system. This blog outlines ten common problems associated with hydraulic hose crimp fittings and provides practical solutions to each. Whether you’re an engineer, maintenance technician, or buyer, this guide will help reduce system downtime, improve safety, and extend the service life of your equipment.
1. Improper Crimping Dimensions
One of the most frequent issues encountered during hydraulic hose crimp fitting assembly is the use of incorrect crimping dimensions. If the crimp diameter is too small, it can exert excessive pressure on the hose, causing damage such as deformation, internal layer delamination, or premature wear. Conversely, if the crimp diameter is too large, the fitting may not secure the hose properly, leading to potential leaks or blow-offs during high-pressure operation. Both extremes threaten the integrity and safety of the hydraulic system.
Solution:
Always use manufacturer-specified crimping dimensions that are precisely tailored for the hose and fitting type. Employ calibrated crimping machines and routinely verify the crimp diameter with precision instruments like micrometers or calipers. Additionally, implement regular maintenance and calibration of crimping equipment to ensure consistent performance. Operator training on correct crimp parameters is essential to minimize human error.
2. Hose Burst Due to Incorrect Fitting Type
Using the wrong type of hydraulic hose crimp fittings for a specific hose or application can lead to catastrophic hose failure under pressure.
Solution:
Before assembly, carefully review the hose manufacturer’s specifications, ensuring fittings match in size, pressure rating, and fluid type. Consulting product catalogs or technical support can provide guidance on compatible fittings. Using fittings certified by industry standards (e.g., SAE, ISO) can also help ensure reliability and safety.
3. Leaking at the Crimped End
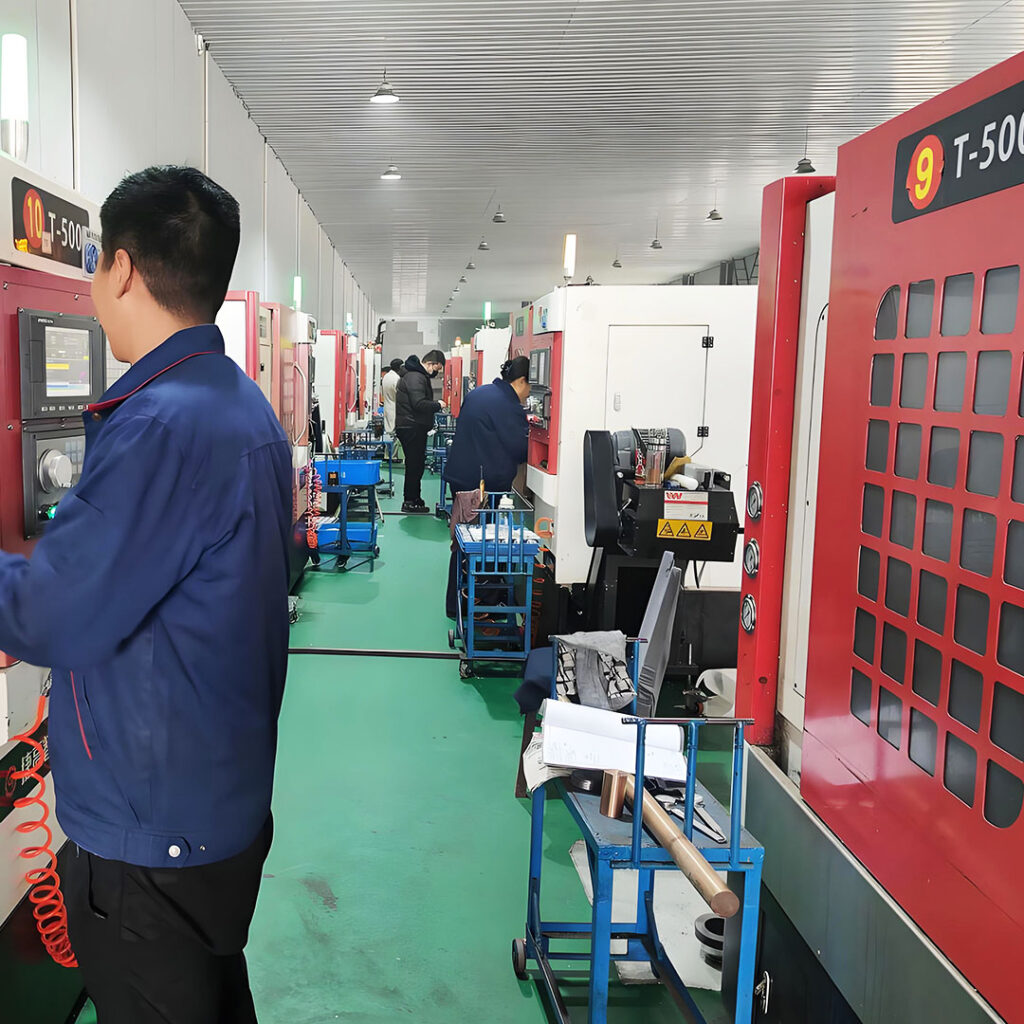
Leaks at the crimped end can be caused by contamination, poor crimp technique, or mismatched components.
Solution:
Establish strict cleanliness protocols during assembly. All parts—hoses, fittings, tools—should be free of dirt, debris, and oil residues. Maintain a clean work environment and wear gloves to prevent contamination. Verify compatibility between hose and fitting materials. Use inspection tools to ensure crimping force and depth meet specifications before system pressurization.
4. Fitting Blow-Offs During Operation
A fitting blow-off is a dangerous failure mode where the fitting separates from the hose during use, often due to insufficient crimp retention.
Solution:
Check for correct crimp depth and make sure the hose is fully inserted into the fitting. Perform pull tests to validate secure assembly.
5. Corrosion of Fitting Surfaces
Corrosion weakens the metal components of hydraulic hose crimp fittings, leading to premature failure, especially in outdoor or marine environments.
Solution:
Use corrosion-resistant materials such as stainless steel or fittings with protective coatings (e.g., zinc plating, powder coating). Store equipment in controlled environments when possible, and perform regular inspections for early signs of corrosion. Applying rust inhibitors or using environmental enclosures can extend fitting life.
6. Incorrect Assembly Sequence
Following the wrong order during assembly can compromise hose integrity. For instance, failing to clean the hose end before fitting insertion or crimping before proper lubrication can cause internal damage or weak crimps.
Solution:
Follow standardized assembly procedures including hose cutting, cleaning, lubrication, and crimping in the correct order.
7. Excessive Wear Due to Vibration
Hydraulic systems often operate in environments with significant vibration and mechanical stress. Constant vibration can loosen fittings, cause abrasion, or lead to micro-leaks that worsen over time.
Solution:
Install vibration dampeners or flexible mounts to absorb mechanical shocks. Properly route and secure hoses to minimize movement. Use abrasion-resistant sleeves where hoses contact rough surfaces. Regularly inspect fittings and hoses for signs of wear or loosening and retighten or replace as needed.
8. Temperature-Related Failures
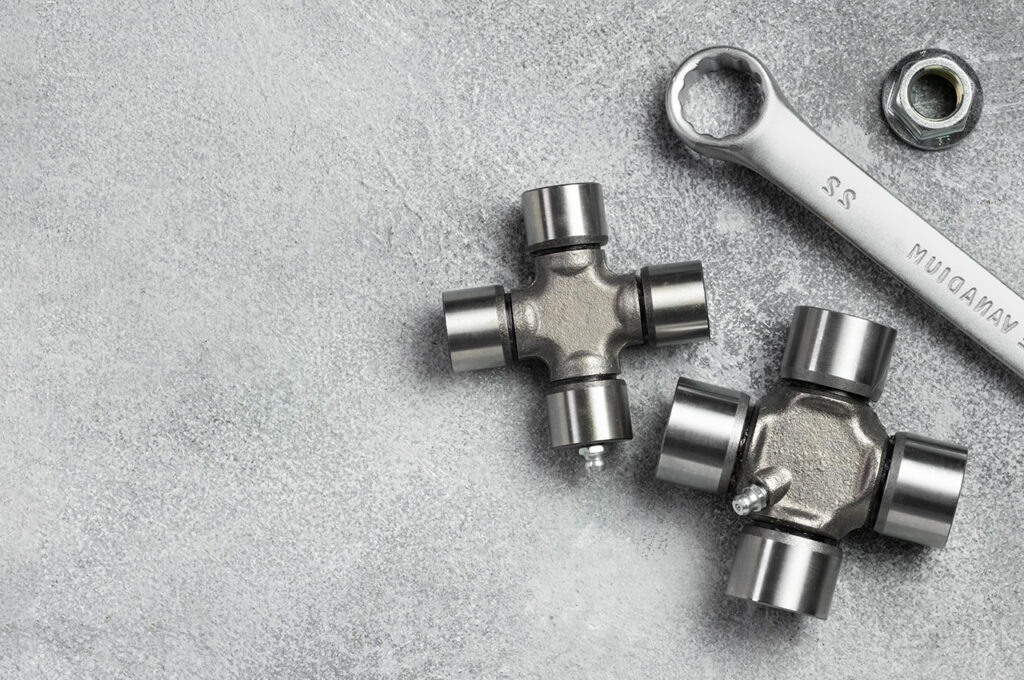
Extreme temperatures, whether hot or cold, affect both the hose material and the fittings. Heat can soften or degrade hose polymers and metals, while cold temperatures can make hoses brittle or cause seals to shrink, leading to cracks or detachment.
Solution:
Select hose and fitting materials rated for the expected temperature range of your application. For hot environments, materials like fluoropolymer or high-temperature rubber may be required. In cold climates, materials that remain flexible at low temperatures are critical. Additionally, use thermal insulation, heat shields, or cooling systems as appropriate.
9. Internal Hose Damage from Insertion
Improper insertion techniques, such as forcing fittings into the hose without lubrication or using incorrect tools, can damage the hose’s inner lining. This weakens the hose’s burst strength and disrupts fluid flow.
Solution:
Always use the correct insertion tools and compatible lubricants to ease fitting installation. Avoid excessive force. Train assembly personnel on proper handling techniques to protect hose internal structure and ensure optimal flow performance.
10. Inventory Confusion and Wrong Part Use
In busy workshops or large operations, it’s common to confuse fittings due to their similar appearance, leading to the wrong part being installed. This can cause mismatched connections, resulting in failures.
Solution:
Implement a clear inventory management system with labeling by part numbers, sizes, and color codes. Use organized storage bins and digital tracking when possible. Regularly audit inventory to prevent mix-ups and train staff on proper part identification.
Hydraulic Hose Crimp Fittings Problem-Solution Summary Table
Problem | Cause | Solution | Risk Level |
---|---|---|---|
Improper crimping dimensions | Wrong settings, uncalibrated tool | Use correct dimensions and calibrate tools | High |
Wrong fitting type | Incompatible with hose or pressure | Match hose and fitting specs | High |
Leaking at crimp | Dirty parts, incorrect technique | Clean environment and proper crimping | Medium |
Fitting blow-off | Shallow crimp, partial insertion | Ensure full insertion and pull test | High |
Fitting corrosion | Harsh environment, material selection | Use stainless steel or coated fittings | Medium |
Incorrect assembly sequence | Skipping or misordering steps | Follow proper procedure | Medium |
Wear from vibration | Poor support or layout | Add dampeners and secure hoses | Medium |
Temperature-related damage | Inappropriate material selection | Choose rated materials and protect surfaces | High |
Internal damage during insertion | Forcing, lack of lubrication | Lubricate and insert properly | Medium |
Inventory confusion | Poor labeling or storage | Organize and label fittings | Low |
Conclusion
Avoiding common problems with hydraulic hose crimp fittings is critical to system safety, efficiency, and longevity. Every failure point—whether it’s a crimping issue, material mismatch, or installation error—can lead to costly downtime and safety hazards. Proactively addressing these concerns through best practices, proper training, and quality control can significantly reduce failure rates.
By identifying the causes of these common problems and applying the right solutions, you can increase system reliability, protect workers, and ensure a longer service life for your hydraulic equipment.
FAQ
What causes fittings to leak after installation?
Leaks in hydraulic hose crimp fittings after installation are commonly caused by several factors, including improper crimping techniques, contamination during assembly, or mismatched components. Improper crimping, such as incorrect crimp diameter or uneven pressure, can prevent the fitting from sealing tightly to the hose, resulting in fluid leaks. Contamination—like dirt, dust, or oil residues—between the fitting and hose surfaces can also compromise the seal. Additionally, using hydraulic hose crimp fittings that are incompatible with the hose material or size often leads to leaks. Therefore, to prevent leakage, it’s critical to carefully check all crimping dimensions, maintain a clean assembly environment, and verify that the hydraulic hose crimp fittings and hoses are fully compatible.
Can hydraulic hose crimp fittings be reused?
In most cases, hydraulic hose crimp fittings are designed for one-time use and should not be reused. Once a hydraulic hose crimp fitting has been crimped onto a hose, the metal fitting permanently deforms to secure the connection. Attempting to remove and reuse the same fitting risks damaging both the fitting and the hose, which can lead to compromised sealing, reduced mechanical strength, and potential safety hazards such as leaks or blow-offs under pressure. For optimal system reliability and safety, always use new hydraulic hose crimp fittings when replacing hoses or performing maintenance.
How often should I inspect hydraulic hose crimp fittings?
Regular inspection of hydraulic hose crimp fittings is vital for maintaining system safety and performance. It is recommended to perform routine visual and physical inspections of hydraulic hose crimp fittings at least once a month. In high-pressure applications or critical systems, more frequent inspections—such as weekly or biweekly—are advisable. Inspections should check for signs of leaks, corrosion, cracking, deformation, or loosening of fittings. Proactive maintenance based on these inspections helps prevent unexpected failures and extends the service life of hydraulic hose crimp fittings.
Are there standards for hydraulic hose crimp fittings?
Yes, hydraulic hose crimp fittings must comply with industry standards to ensure safety, performance, and interchangeability. The Society of Automotive Engineers (SAE) and the International Organization for Standardization (ISO) both publish comprehensive standards defining the design, dimensions, pressure ratings, materials, and testing methods for hydraulic hose crimp fittings. Adhering to these standards helps manufacturers produce fittings that reliably match hoses and perform safely under specified operating conditions. Users should always verify that their hydraulic hose crimp fittings meet relevant SAE or ISO standards appropriate for their application.
What is the typical lifespan of hydraulic hose crimp fittings?
The lifespan of hydraulic hose crimp fittings varies widely depending on factors such as operating pressure, temperature, exposure to corrosive environments, and quality of installation. Generally, well-installed hydraulic hose crimp fittings can last several years under normal operating conditions. However, exposure to extreme temperatures, aggressive chemicals, vibration, or mechanical abrasion can shorten their service life. Regular inspection and maintenance are crucial to detect early signs of wear or damage. Replacing hydraulic hose crimp fittings proactively before failure ensures system reliability and prevents costly downtime.