Table of Contents
Introduction
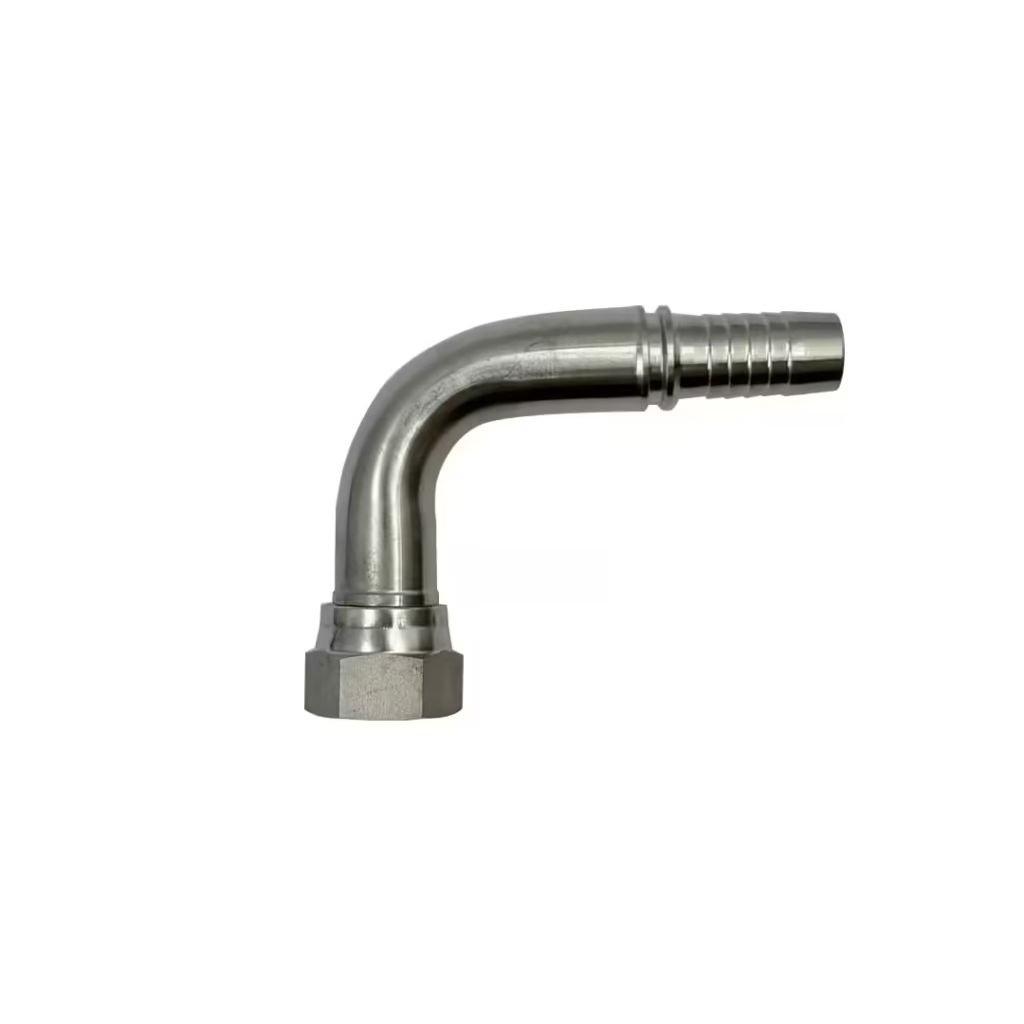
Gates hydraulic fittings are vital components in hydraulic systems, playing a crucial role in ensuring secure connections and efficient fluid flow. These fittings are widely used across industries such as manufacturing, automotive, agriculture, and construction, where hydraulic machinery relies on reliable parts to function optimally.
The quality and design of gates hydraulic fittings directly impact the performance, durability, and safety of hydraulic systems. Choosing the right fittings can prevent leaks, reduce downtime, and improve system efficiency. This article explores the 10 essential features of gates hydraulic fittings, highlighting why they are favored and what makes them indispensable for any hydraulic application.
Feature 1: Superior Material Quality in Gates Hydraulic Fittings
The first essential feature of gates hydraulic fittings lies in their use of premium, high-grade materials carefully selected to meet the demanding requirements of hydraulic systems. Typically, these fittings are manufactured from stainless steel, carbon steel, or brass—each chosen for its unique properties that contribute to long-term durability and operational reliability.
Stainless steel offers excellent corrosion resistance, especially in harsh chemical or marine environments, preventing rust and surface degradation that could compromise system integrity. Carbon steel is prized for its strength and toughness, providing superior resistance to mechanical stress and high pressure. Brass, known for its excellent machinability and moderate corrosion resistance, is often utilized in lower-pressure or specialized applications.
Beyond just material choice, gates hydraulic fittings adhere to stringent international quality standards, such as ISO and SAE certifications. These certifications ensure that the materials withstand extreme stress, pressure spikes, and temperature variations without losing structural integrity. This rigorous material selection process guarantees that the fittings deliver reliable performance, minimize maintenance needs, and prolong the service life of the entire hydraulic system, even when exposed to fluctuating environmental conditions.
Feature 2: Precision Engineering and Design of Gates Hydraulic Fittings
Precision engineering is a defining hallmark of gates hydraulic fittings and critical to their superior performance. Every fitting undergoes meticulous design processes, where advanced CAD software and computer numerical control (CNC) machining are employed to achieve exceptionally tight tolerances and dimensional accuracy.
This precision ensures a perfect, leak-proof seal when fittings are assembled with hoses or tubes, minimizing the risk of hydraulic fluid leaks that can lead to downtime, environmental hazards, or system damage. Moreover, smooth internal surfaces are engineered to reduce turbulence and friction within the fluid flow, improving overall hydraulic efficiency and reducing energy loss in the system.
The design philosophy also prioritizes compatibility with a wide range of hose sizes, tube diameters, and thread standards. Whether operating in metric or imperial units, or working with different thread types such as BSP, NPT, or JIC, gates hydraulic fittings offer universal adaptability. This versatility simplifies system design and maintenance, enabling seamless integration into diverse hydraulic machinery across various industries.
Feature 3: Robust Pressure Handling Capability in Gates Hydraulic Fittings
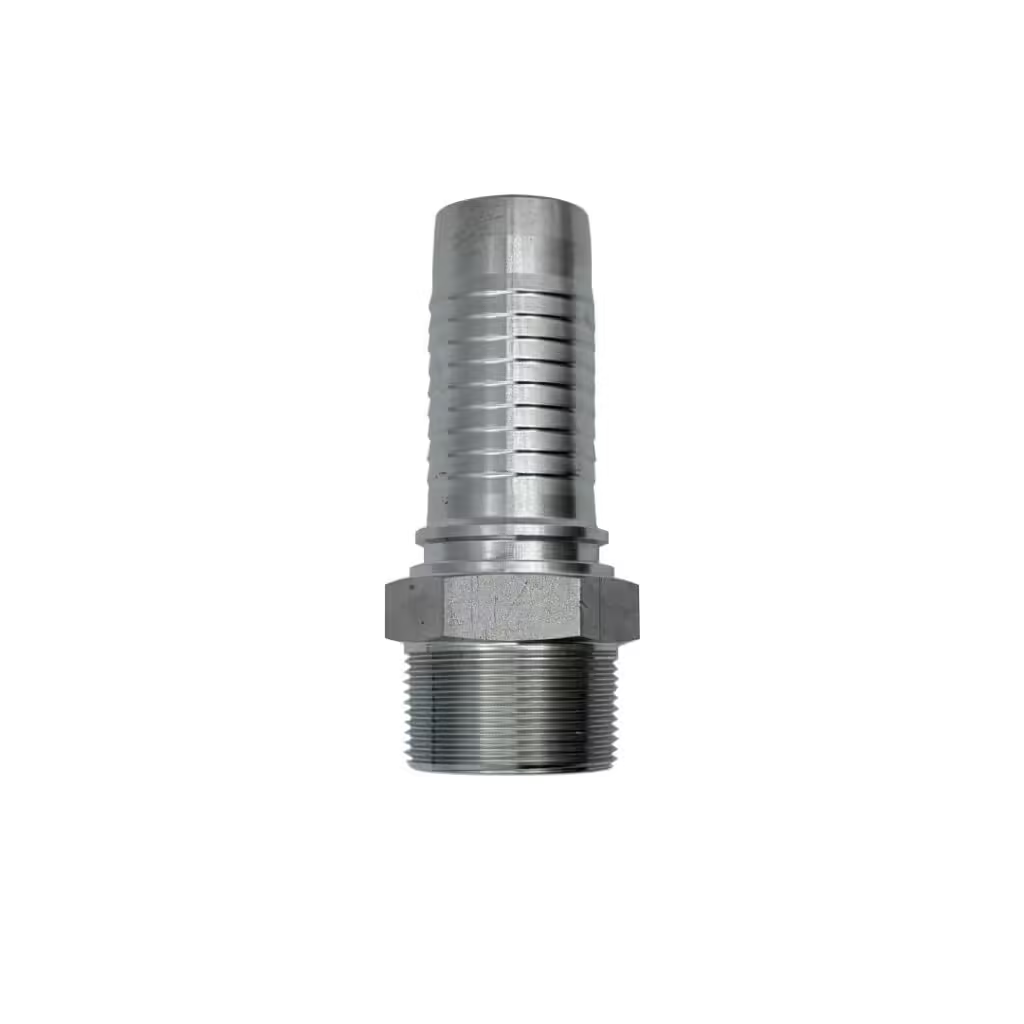
Gates hydraulic fittings are engineered to withstand the demanding pressure conditions characteristic of modern hydraulic systems. Hydraulic machinery can operate under extremely high pressures—often ranging from hundreds to thousands of pounds per square inch (psi)—and fittings must be designed to maintain safety and reliability under such stress.
Each gates hydraulic fitting undergoes rigorous testing and certification to validate its pressure rating. These ratings are prominently specified, enabling engineers and operators to select fittings that precisely match or exceed their system’s pressure requirements. The robust construction, which often includes reinforced bodies and hardened surfaces, prevents deformation, cracking, or failure when exposed to intense pressure.
This high-pressure tolerance ensures that hydraulic systems maintain continuous, leak-free operation even in the most challenging industrial environments such as construction equipment, heavy machinery, and manufacturing plants. Reliable pressure handling reduces risks of accidents and costly repairs, enhancing overall operational safety and productivity.
Feature 4: Corrosion Resistance for Longevity of Gates Hydraulic Fittings
Corrosion resistance is a vital characteristic of gates hydraulic fittings, especially for applications where exposure to moisture, chemicals, or harsh outdoor elements is inevitable. Gates employs corrosion-resistant alloys, specialized surface treatments, and protective coatings—such as zinc plating or chrome finishing—to safeguard the fittings against rust and chemical attack.
This corrosion protection prevents premature material degradation, which can cause leaks, contamination, or catastrophic system failures. Furthermore, corrosion-resistant fittings help maintain the purity of hydraulic fluids by preventing rust particles or other contaminants from entering the system, which could otherwise damage pumps, valves, or cylinders.
Industries like marine, agriculture, mining, and chemical processing especially benefit from this feature, as these environments present challenging conditions such as saltwater exposure, acidic compounds, or abrasive dust. By resisting corrosion, gates hydraulic fittings significantly extend the service life of hydraulic components, lower maintenance costs, and improve system reliability under tough operating conditions.
Feature 5: Ease of Installation and Maintenance
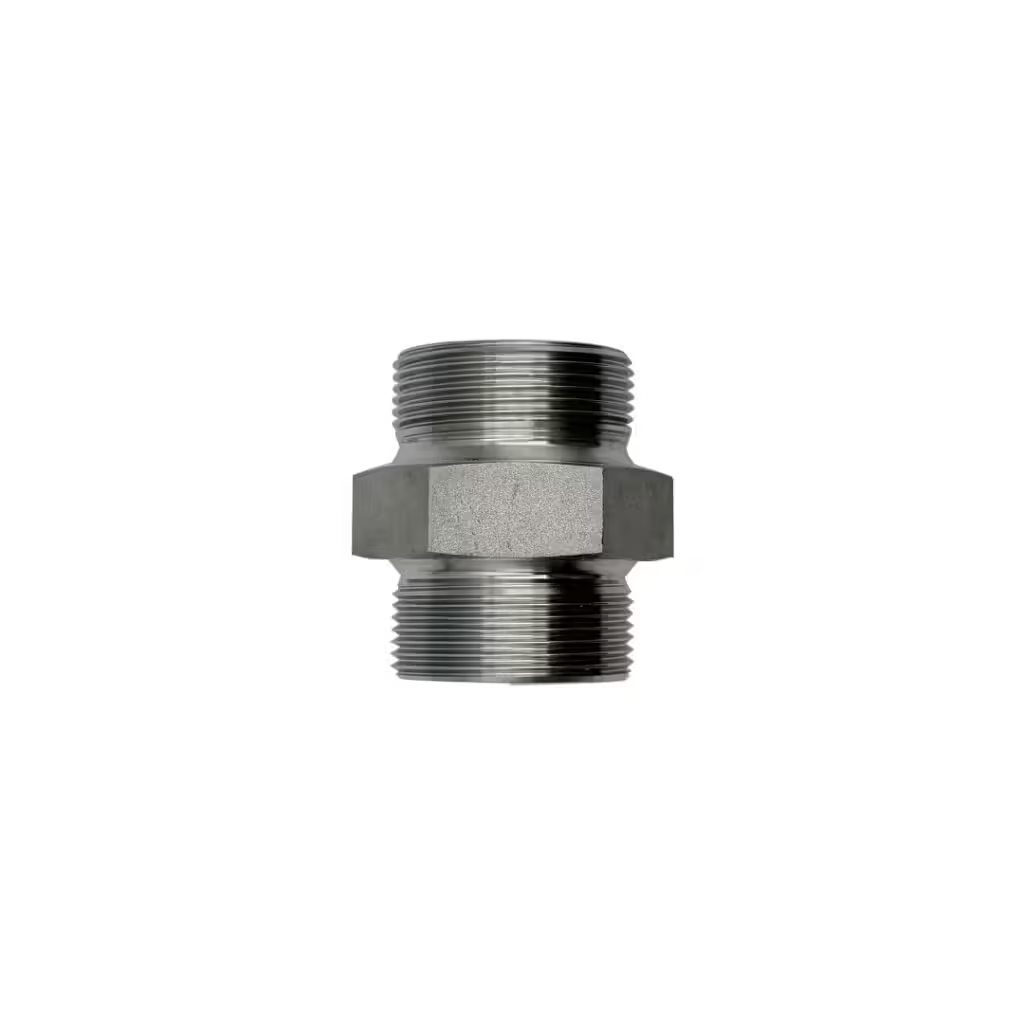
Gates hydraulic fittings are designed not only for performance but also for convenience, emphasizing ease of installation and routine maintenance to reduce downtime and operational costs. Their user-friendly design often includes standardized thread patterns, quick-connect options, and reusable sealing elements such as O-rings or metal-to-metal seals.
This simplicity means technicians can assemble and disassemble fittings quickly, often using common hand tools without requiring specialized equipment. Reduced installation complexity shortens setup times and minimizes the risk of improper assembly, which could lead to leaks or system failures.
Moreover, many gates hydraulic fittings incorporate design features that facilitate maintenance, such as replaceable seals and corrosion-resistant surfaces that simplify cleaning and inspection. This approach allows maintenance teams to perform repairs or replacements rapidly, reducing machine idle time and ensuring hydraulic systems remain operational with minimal disruption.
Overall, the focus on ease of installation and maintenance supports higher productivity and lowers total cost of ownership for users across industries.
Mid-Article Table: Comparison of Key Gates Hydraulic Fittings Features
Feature | Description | Benefit |
---|---|---|
Material Quality | Stainless steel, carbon steel, brass | Durability, corrosion resistance |
Precision Engineering | CNC machining, tight tolerances | Leak prevention, efficient flow |
Pressure Handling Capacity | Rated for high-pressure environments | Safety, system reliability |
Corrosion Resistance | Coatings and alloys | Extended service life |
Ease of Installation | Quick assembly, reusable seals | Reduced labor costs and downtime |
Compatibility | Various thread and hose sizes | Flexible system integration |
Temperature Tolerance | Operates under extreme temperatures | Wide application range |
Vibration and Shock Resistance | Robust design to absorb shocks | Prevents premature failure |
Sealing Technology | Advanced seal designs | Leak-proof connections |
Compliance and Certification | Meets international standards | Assurance of quality and safety |
Feature 6: Compatibility with Various Hydraulic Systems
Gates hydraulic fittings are designed to be compatible with a wide range of hydraulic hoses, tubes, and machinery. This versatility allows them to be used in different applications without requiring specialized adapters. Compatibility ensures that systems can be built or upgraded efficiently, reducing the complexity of inventory management.
The fittings support multiple thread standards such as BSP, NPT, and metric threads, catering to both regional and global markets. This universal compatibility is crucial for multinational operations and industries that require standardized parts.
Feature 7: Temperature Resistance of Gates Hydraulic Fittings
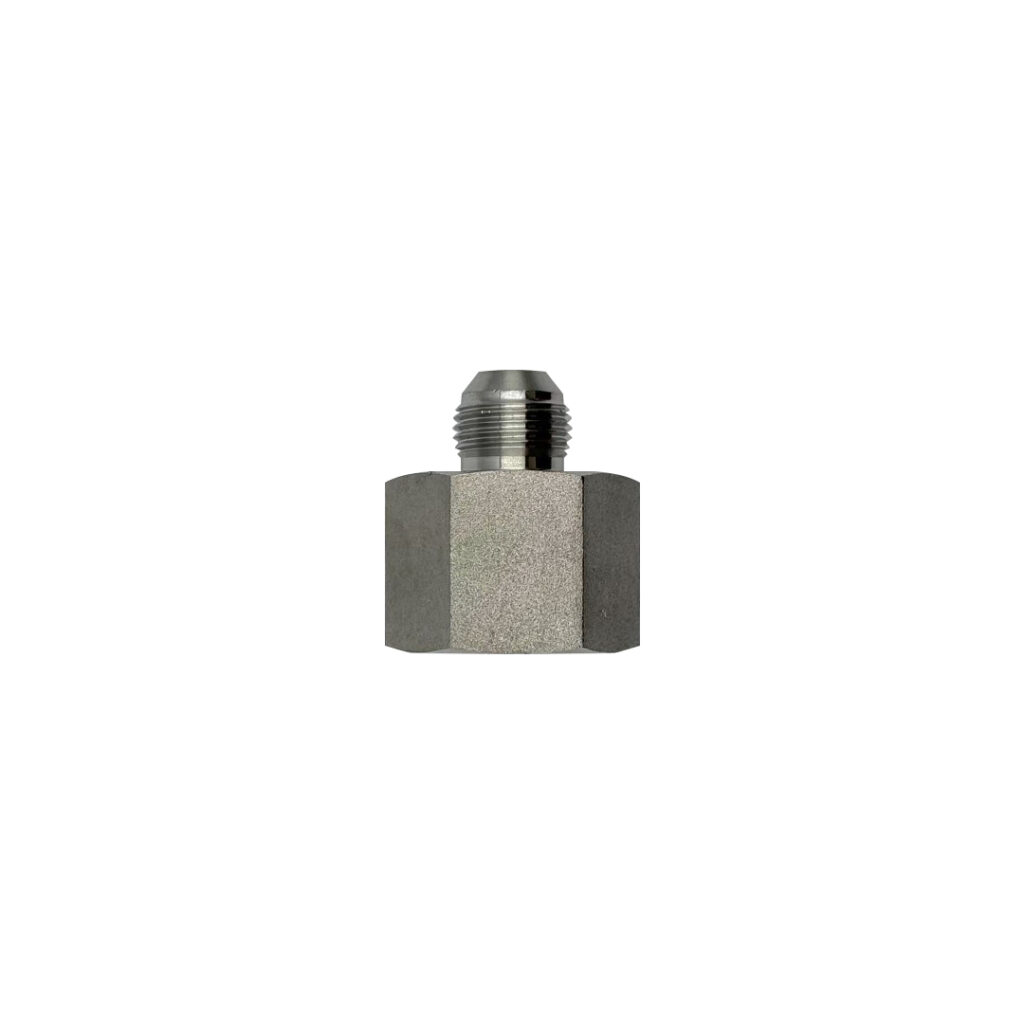
Hydraulic systems often operate in environments with extreme temperature variations. Gates hydraulic fittings are engineered to withstand both high and low temperatures without losing integrity or sealing ability. Materials and seals are chosen to maintain performance even in freezing cold or scorching heat.
Temperature resistance ensures that fittings do not crack, deform, or leak when exposed to harsh conditions, thereby protecting the hydraulic system’s efficiency and safety.
Feature 8: Vibration and Shock Resistance
In industrial applications, hydraulic fittings may be subject to continuous vibration and sudden shocks. Gates hydraulic fittings incorporate robust designs that absorb and resist these mechanical stresses, preventing loosening or damage over time.
This feature is vital in mobile machinery, heavy equipment, and other dynamic environments where vibration is unavoidable. Proper vibration resistance extends the life of the fittings and reduces maintenance needs.
Feature 9: Advanced Sealing Technology
The sealing mechanism in hydraulic fittings is critical to prevent leaks. Gates hydraulic fittings often utilize cutting-edge seal materials and designs such as O-rings, metal-to-metal seals, and face seals to ensure leak-proof connections.
These seals are engineered to maintain contact and elasticity even under fluctuating pressures and temperatures. Reliable sealing contributes to system safety, reduces fluid loss, and prevents environmental contamination.
Feature 10: Compliance with International Standards and Certifications
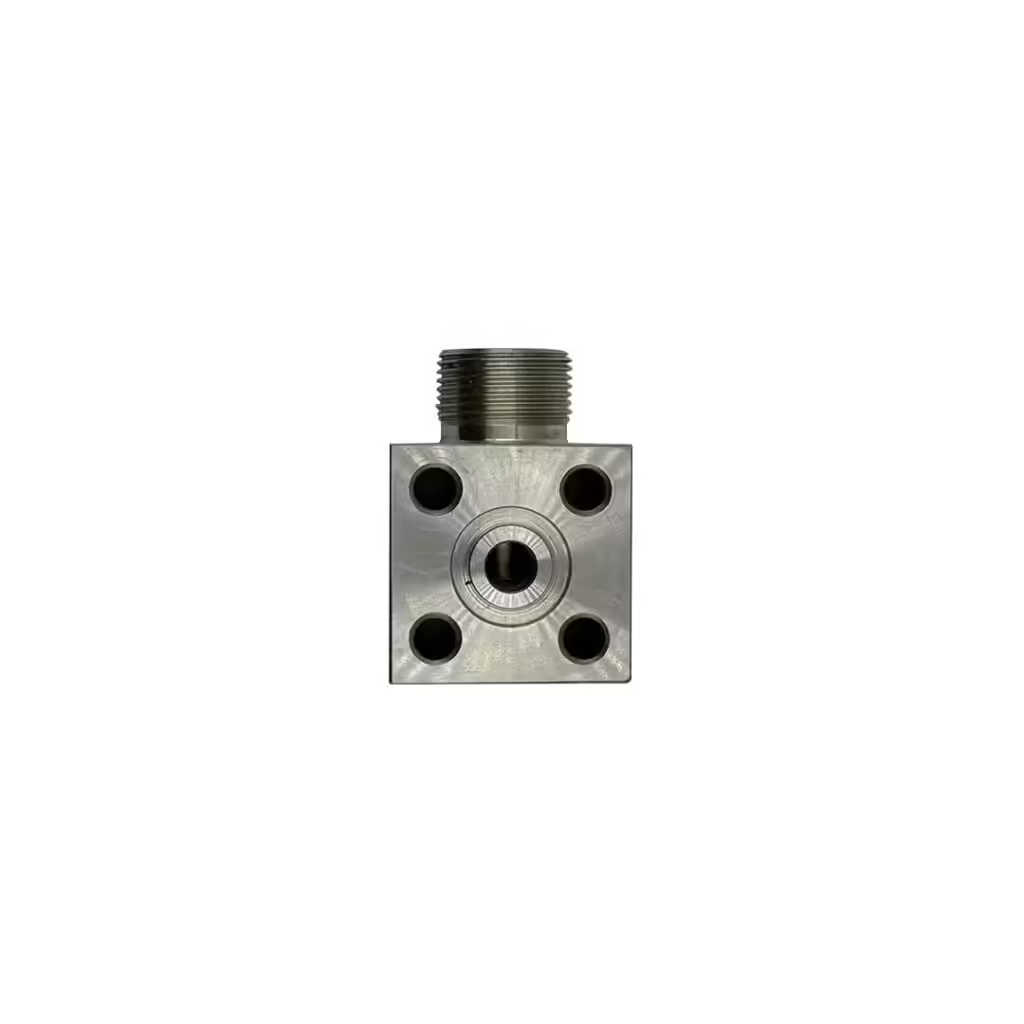
Quality assurance through compliance with industry standards is a defining feature of gates hydraulic fittings. These fittings meet or exceed requirements set by organizations such as SAE, ISO, and DIN, providing users with confidence in their safety and performance.
Certification also facilitates international trade and ensures fittings are suitable for use in regulated industries, such as aerospace, automotive, and manufacturing.
Conclusion
Gates hydraulic fittings offer a combination of features that make them essential for reliable, efficient, and safe hydraulic systems. From superior material quality and precision engineering to advanced sealing and compliance with standards, these fittings are designed to meet the rigorous demands of modern industries.
Understanding these 10 essential features helps users select the right fittings for their applications, ensuring system longevity, minimizing downtime, and maintaining optimal performance. Whether upgrading existing systems or designing new ones, investing in high-quality gates hydraulic fittings is a smart choice that pays off in reliability and efficiency.
FAQ
What are gates hydraulic fittings used for?
They are used to connect hoses, tubes, and components in hydraulic systems, ensuring secure and leak-free fluid transfer.
How do I select the right gates hydraulic fittings?
Consider pressure ratings, compatibility, material type, sealing mechanism, and operating environment when choosing fittings.
Can gates hydraulic fittings handle extreme temperatures?
Yes, many are designed to function reliably under both high and low temperature conditions.
Are gates hydraulic fittings easy to install?
Yes, they are engineered for straightforward installation and maintenance, often requiring minimal tools.
Why is sealing technology important in hydraulic fittings?
Proper sealing prevents leaks, fluid loss, and contamination, maintaining system efficiency and safety.