Table of Contents
Introduction
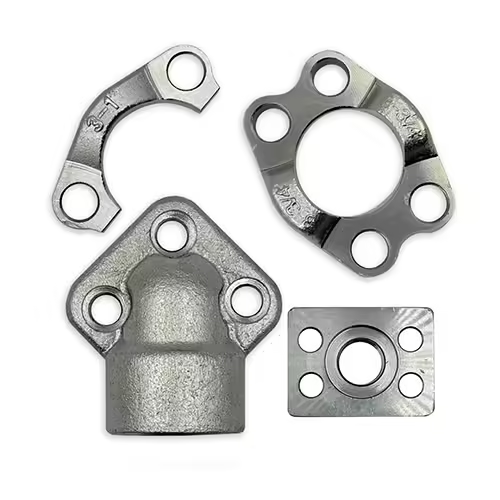
Flanged fittings, including flange clamps, flange couplings, and flange joints, play a vital role in securing and sealing hydraulic and piping systems. Choosing the right flanged fittings can directly affect a system’s reliability, efficiency, and maintenance requirements. Whether you’re sourcing for high-pressure hydraulic systems or industrial pipelines, selecting the appropriate fittings ensures performance and safety.
This guide outlines 10 smart tips for selecting flanged fittings, especially for manufacturers and buyers in sectors like hydraulics, oil and gas, water treatment, and heavy machinery. We’ll also showcase products from Hebei Minglai Pipe Fitting Co., Ltd., a professional manufacturer known for high-quality, customizable hydraulic joints and flanged fittings.
Tip 1: Understand the Application Requirements
Before selecting flanged fittings, it’s essential to have a clear understanding of your system’s technical demands. This includes the operating pressure, fluid type, temperature range, and installation environment. For example, if your system handles highly corrosive chemicals or operates under high pressure, you’ll need flanged fittings designed with durable and resistant materials like stainless steel or special alloys.
Different applications demand different design specifications. In medium to high-pressure hydraulic systems, SAE standard flanged fittings are often preferred because they ensure strong, leak-proof connections. For chemical processing or marine systems, fittings with enhanced corrosion resistance are a must.
Being precise with your operating conditions will help you avoid premature failures, system downtime, or costly retrofitting later.
Tip 2: Choose the Right Flange Type
Selecting the correct type of flanged fitting can significantly impact the safety, efficiency, and cost-effectiveness of your piping system. Common types include:
- Weld Neck Flanges: These are ideal for high-pressure applications where structural integrity is crucial. The long neck provides reinforcement, making them suitable for harsh environments.
- Slip-On Flanges: Easier to install and align, these are best suited for low-pressure, non-critical systems.
- Threaded Flanges: These are used in environments where welding is impractical or prohibited, such as explosive or flammable atmospheres.
- Socket Weld Flanges: Ideal for small-diameter piping and high-pressure systems. They offer excellent sealing properties.
- Blind Flanges: Used to terminate or isolate piping systems, providing easy access for future maintenance or extensions.
When choosing among these, consider compatibility with pipe material, flow requirements, and the overall system design. Using the wrong type can cause misalignment, stress fractures, or leakage.
Tip 3: Match Standards and Dimensions Correctly
One of the most overlooked but vital factors in selecting flanged fittings is ensuring compliance with recognized international standards. Standards such as ANSI/ASME, ISO, and SAE ensure that your components will function properly and fit securely.
Each flange has specific dimension requirements—outer diameter, bolt circle diameter (BCD), number and size of bolt holes, and thickness. Mismatching even one dimension can result in serious mechanical issues or system failure. Therefore, ensure dimensional compatibility across all connected components.
Consult dimension charts and pressure rating tables before making a purchase, especially if you are integrating parts from multiple manufacturers or global suppliers.
Tip 4: Prioritize Material Quality
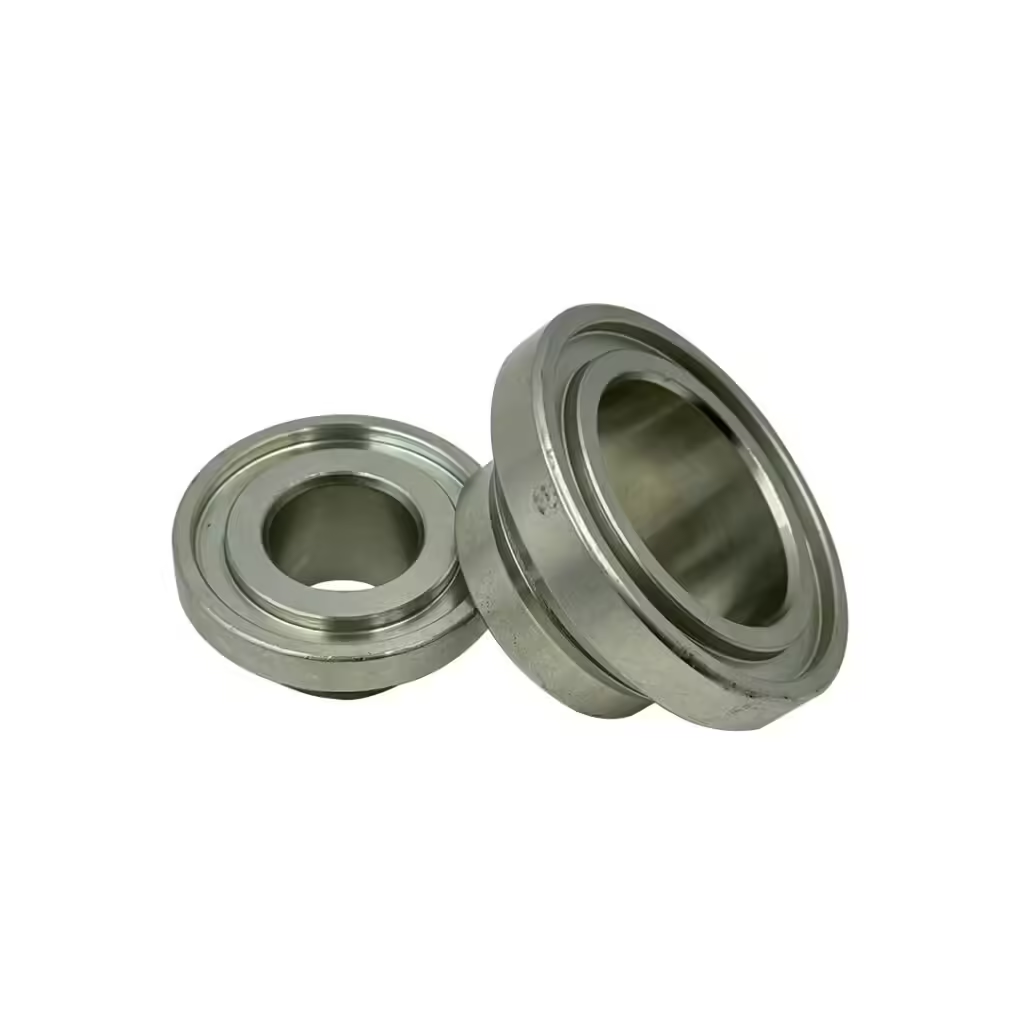
The material of your flanged fittings has a direct impact on their durability, corrosion resistance, and temperature tolerance. Common materials include:
- Carbon Steel: Ideal for general industrial use, offering a good balance between strength and cost.
- Stainless Steel: Highly resistant to corrosion and suitable for food-grade, marine, and chemical applications.
- Alloy Steels: Used in applications requiring extreme strength or temperature resistance.
- PVC or CPVC: Suitable for non-metallic applications and highly resistant to a wide range of chemicals.
For critical systems, choose manufacturers that offer full material certifications and testing documentation, such as mill test reports. For example, Hebei Minglai Pipe Fitting Co., Ltd. provides fittings crafted from certified materials, verified through comprehensive mechanical and chemical testing. This ensures long-term reliability in demanding environments.
Tip 5: Look for Advanced Manufacturing and Testing
Not all flanged fittings are created equal. High-quality fittings are produced through precision forging, CNC machining, and stringent quality control procedures. Advanced manufacturing methods help maintain tight dimensional tolerances and surface finishes that are essential for proper sealing.
Quality flanged fittings also undergo various forms of testing, including:
- Hydrostatic Pressure Testing: Ensures pressure integrity.
- Non-Destructive Testing (NDT): Includes ultrasonic, radiographic, or magnetic particle testing to detect internal flaws.
- Hardness and Tensile Testing: Measures material strength and resistance.
Choosing a supplier with modern testing facilities helps minimize risk and ensures that the flanged fittings will perform reliably in real-world conditions. This is particularly important for systems where safety and uptime are critical.
Tip 6: Compare Popular Flanged Fitting Types
Flanged Fitting Type | Pressure Range | Suitable For | Installation | Material Options |
---|---|---|---|---|
SAE Flange Clamp | Medium–High | Hydraulics | Bolt-on | Carbon/Stainless |
Threaded Flange | Low–Medium | Gas, Water | Easy | Carbon Steel |
Weld Neck Flange | High | Oil & Gas | Welded | Alloy Steel |
Slip-On Flange | Low | Water Lines | Slip-fit | Stainless Steel |
This table helps you evaluate different options based on application needs and installation ease.
Tip 7: Evaluate Sealing Mechanisms
Good sealing prevents leaks, contamination, and system failure. Choose flanged fittings that provide consistent compression and surface contact. The use of high-quality gaskets and correct torque application also enhances sealing reliability.
Tip 8: Check for Corrosion Resistance
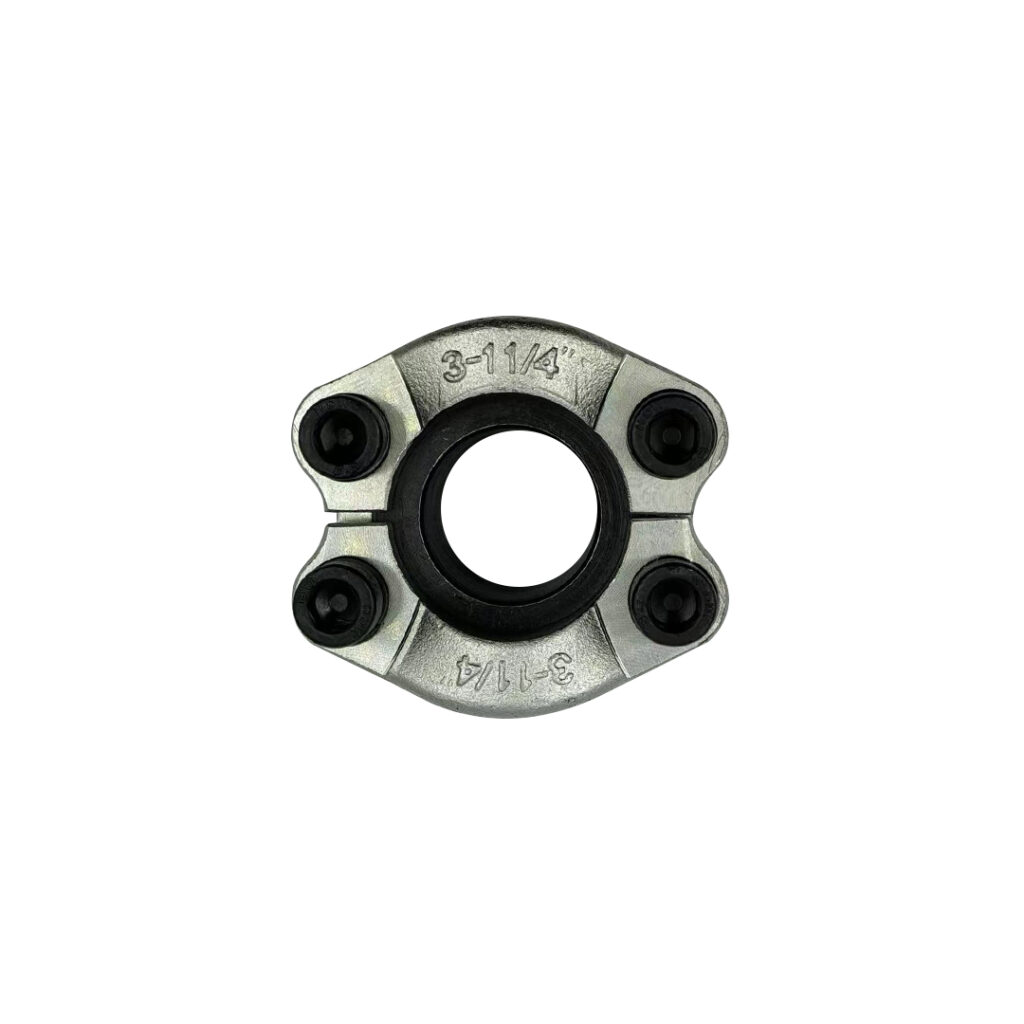
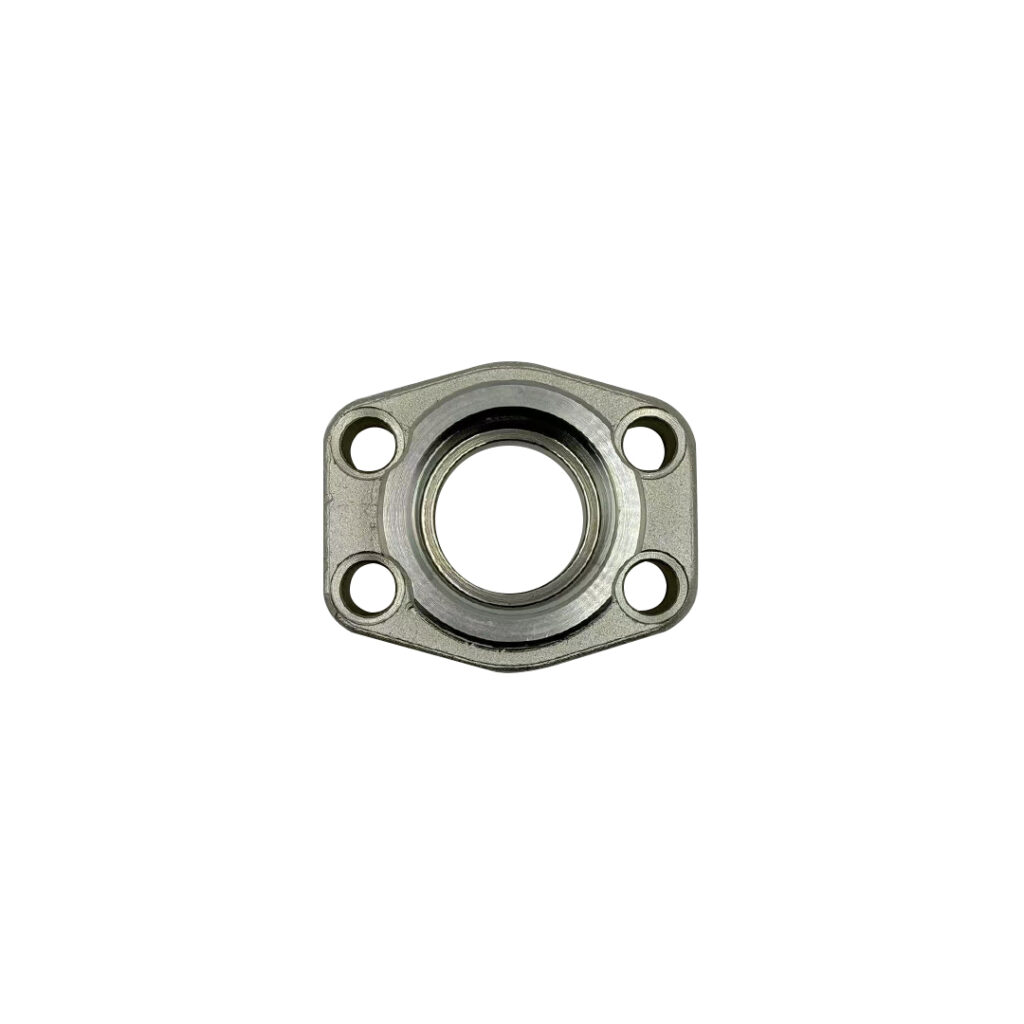
In harsh environments, corrosion resistance is crucial. Stainless steel is a strong performer against rust and chemical damage. For added protection, surface treatments like galvanizing or powder coating may be applied.
Tip 9: Verify After-Sales Support and Customization Options
Work with suppliers who offer technical assistance, documentation, and customization. Hebei Minglai Pipe Fitting Co., Ltd. provides tailored flanged fittings solutions for unique hydraulic systems, along with comprehensive after-sales support.
Tip 10: Confirm Delivery Times and Inventory
Production delays can stall your project. Make sure the supplier has sufficient inventory and can meet your timeline. Minglai’s efficient manufacturing processes and scalable production help meet bulk orders quickly without compromising quality.
Conclusion
Choosing the right flanged fittings is not just a technical decision—it’s a strategic one. The correct fittings minimize leaks, reduce downtime, and ensure system safety. By following these 10 tips, industrial buyers can avoid common pitfalls and improve long-term performance.
Hebei Minglai Pipe Fitting Co., Ltd. stands out with its certified materials, strict quality control, and customizable solutions. Whether you’re sourcing standard SAE flange clamps or unique flange joint designs, we’re ready to support your hydraulic system needs.
FAQ
What are flanged fittings used for?
Flanged fittings are used to connect, seal, or fasten pipes in hydraulic or industrial systems, ensuring a secure and leak-proof link.
Are SAE flanged fittings compatible with high-pressure systems?
Yes. SAE flanged fittings are specifically designed for medium to high-pressure hydraulic systems and offer excellent sealing performance.
How can I tell if a flanged fitting meets quality standards?
Check for compliance with SAE, ANSI, or ISO standards, and ask for material certifications and pressure test results from the supplier.
Can I request custom flanged fittings from Minglai?
Absolutely. Hebei Minglai Pipe Fitting Co., Ltd. specializes in both standard and non-standard hydraulic joints, including custom flanged fittings.
How do I choose between carbon steel and stainless steel fittings?
Carbon steel is cost-effective and strong, while stainless steel provides better corrosion resistance. Choose based on environment and budget.