Table of Contents
Introduction
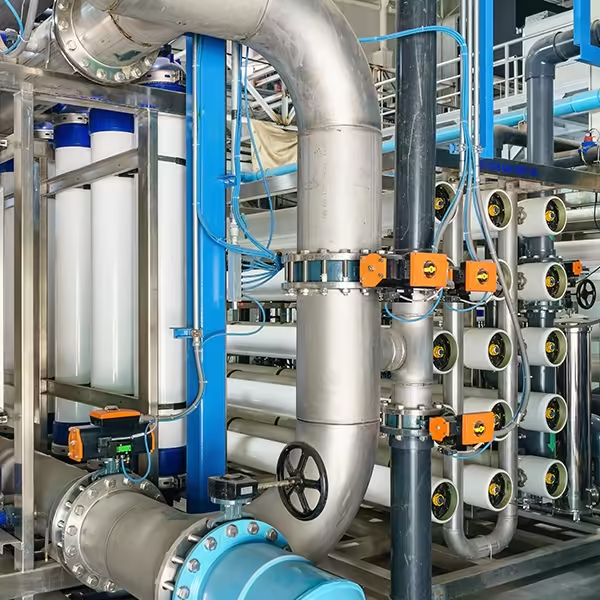
In industrial applications, plumbing, and manufacturing, the use of 316 stainless fittings has become increasingly popular due to their remarkable resistance to corrosion, durability, and ability to withstand harsh environments. These fittings are typically used in marine, chemical, and food processing industries where exposure to chemicals and saltwater is prevalent. Maintaining these fittings properly is crucial to prolong their lifespan and ensure system reliability.
316 stainless steel is an alloy that includes molybdenum, which significantly improves corrosion resistance compared to other stainless steel grades like 304. This unique feature makes 316 stainless fittings a preferred choice for demanding applications. However, without proper maintenance, even the best materials can deteriorate.
This blog will guide you through five vital tips to maintain your 316 stainless fittings effectively, ensuring they continue to perform optimally for years.
Understanding the Material: What Makes 316 Stainless Fittings Unique?
Before diving into maintenance tips, it is essential to understand the characteristics of 316 stainless fittings that influence how you should care for them.
- Corrosion Resistance: The molybdenum content in 316 stainless steel provides excellent resistance to chloride-induced corrosion, making these fittings ideal for salty or chemical-laden environments.
- Durability: 316 stainless fittings exhibit high tensile strength and toughness, making them durable under pressure and mechanical stress.
- Temperature Resistance: They can withstand high temperatures up to 870°C (1600°F) intermittently and 925°C (1700°F) continuously without losing structural integrity.
- Non-Magnetic Properties: Unlike some stainless steels, 316 stainless fittings are mostly non-magnetic, an essential feature for specific electronic and mechanical applications.
These properties dictate that maintenance approaches must be suited to preserve these advantages without causing damage or unnecessary wear.
Tip 1: Regular Cleaning of 316 Stainless Fittings to Prevent Contamination
One of the most fundamental yet often overlooked steps to maintain 316 stainless fittings is consistent and thorough cleaning. Over time, various contaminants such as dirt, grime, salt deposits, and chemical residues can accumulate on the surface of these fittings. Even though 316 stainless steel is known for its excellent corrosion resistance, these deposits, if left unchecked, may promote localized corrosion, discoloration, and eventually reduce the structural integrity of the fittings.
Recommended Cleaning Methods
- Warm Water with Mild Detergents: A simple solution of warm water mixed with a mild detergent is often sufficient for routine cleaning. This method effectively removes surface dirt and oils without damaging the stainless steel.
- Specialized Stainless Steel Cleaners: For more stubborn stains, such as those caused by mineral deposits or industrial pollutants, specialized stainless steel cleaning products can be used. These cleaners are formulated to restore the shine and protective oxide layer without being abrasive.
- Avoid Abrasive Cleaning Tools: It is important to avoid steel wool, wire brushes, or scouring pads that are too rough. These can scratch the surface of the fittings, creating micro-crevices where corrosion can initiate. Instead, opt for soft cloths or non-abrasive sponges.
- Rinse Thoroughly: After cleaning, rinse fittings with clean water to ensure all detergent or cleaning agent residues are removed. Residual chemicals left on the fittings can themselves cause damage over time.
Frequency of Cleaning
- In highly corrosive environments such as marine applications, fittings should be cleaned every 1-2 weeks.
- For less aggressive environments, monthly cleaning may suffice.
Proper cleaning not only maintains the appearance but also extends the life of the fittings by reducing corrosion risks.
Tip 2: Inspection and Detection of Early Signs of Wear or Corrosion
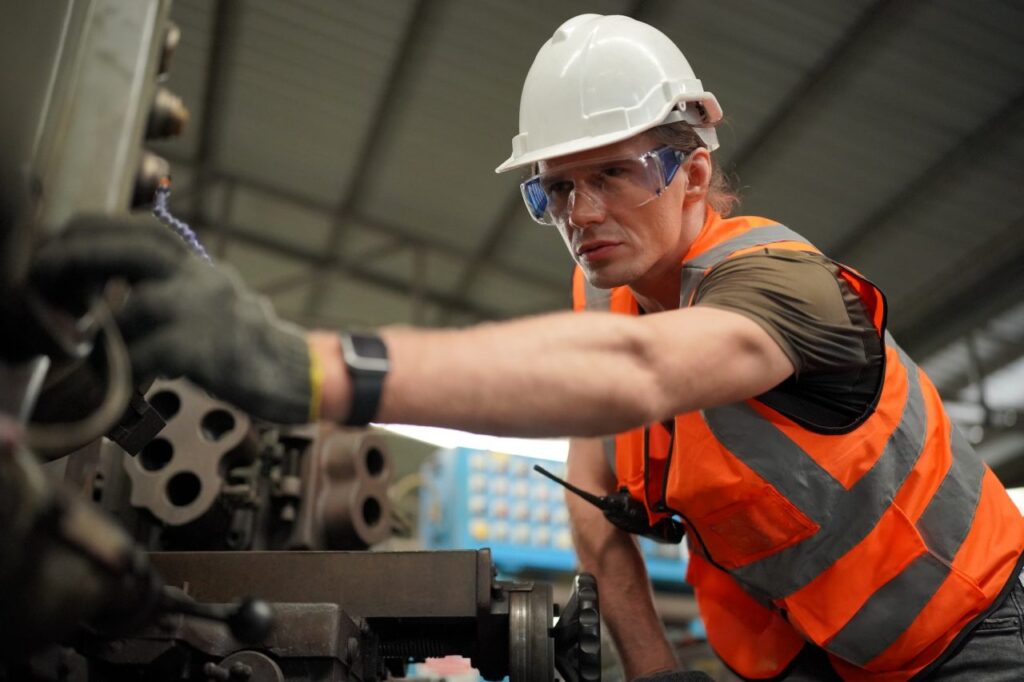
Cleaning alone cannot guarantee the longevity of 316 stainless fittings without regular inspections. Maintenance personnel must perform systematic and thorough inspections to detect early signs of wear, corrosion, or mechanical damage. Early detection is vital to prevent catastrophic failures and costly downtime.
What to Look For
- Pitting or localized corrosion spots, which often appear as tiny holes or discoloration.
- Surface cracks or dents due to mechanical impact.
- Loose fittings or threads that can affect the integrity of the pipeline.
Inspection Tools
- Visual Inspection: The simplest and most cost-effective method involves carefully examining the fittings under good lighting. Use white light sources to avoid color distortions.
- Magnification Tools: Handheld magnifying glasses or portable microscopes allow maintenance teams to examine small areas for pitting or surface damage.
- Borescopes or Fiberscopes: These tools are invaluable for inspecting internal surfaces of fittings and pipes without dismantling.
- Ultrasonic Thickness Gauges: These non-destructive devices measure the remaining metal thickness to detect thinning caused by corrosion or wear.
- Dye Penetrant Inspection (DPI): This non-destructive test highlights surface cracks and flaws that are not visible to the naked eye.
Documenting inspection results helps track the condition over time and plan preventive actions.
Tip 3: Proper Installation Practices to Maintain 316 Stainless Fittings
Effective maintenance of 316 stainless fittings starts at the installation stage. Incorrect installation can create conditions that accelerate wear, promote leaks, and increase maintenance frequency.
Installation Guidelines
- Use Compatible Sealing Materials: Employ PTFE (Teflon) tapes, gaskets, or sealants specifically rated for stainless steel and the system’s fluid. This ensures tight seals without chemical reactions that degrade either the fittings or sealing components.
- Avoid Over-Tightening: Applying excessive torque can deform threads, distort fitting bodies, or cause stress fractures. Follow manufacturer torque specifications carefully using calibrated torque wrenches.
- Ensure Proper Alignment: Misaligned fittings place undue mechanical stress on joints and pipes, increasing wear and risk of cracks or leaks. Use alignment tools or guides to achieve correct positioning during assembly.
- Use Correct Tools: Avoid using pliers or adjustable wrenches that can mar the fitting surface. Use stainless steel-specific tools or protective jaw covers to prevent surface damage.
- Prevent Cross-Threading: Start threading fittings by hand before tightening with tools to avoid cross-threading, which damages both fittings and pipes.
- Lubricate Threads if Recommended: Some installations benefit from anti-seize lubricants designed for stainless steel to prevent galling and ease future disassembly.
Correct installation helps prevent leaks and mechanical failures, reducing the frequency of maintenance.
Middle Section: Table Comparing 316 Stainless Fittings to Other Common Stainless Steel Fittings
Here is a detailed comparison table to understand the advantages of 316 stainless fittings compared to other common stainless steel fittings like 304 and 310.
Property | 316 Stainless Fittings | 304 Stainless Fittings | 310 Stainless Fittings |
---|---|---|---|
Corrosion Resistance | Excellent, especially against chlorides | Good, less resistant to chlorides | Moderate, better at high temperatures |
Molybdenum Content | 2-3% | None | None |
Temperature Resistance | Up to 870°C intermittent | Up to 870°C intermittent | Up to 1150°C continuous |
Magnetic Properties | Mostly non-magnetic | Non-magnetic | Non-magnetic |
Common Applications | Marine, chemical, food processing | Food, beverage, construction | High-temperature environments |
Cost | Higher | Lower | Higher |
This table highlights why 316 stainless fittings are often the preferred choice for corrosive environments despite a slightly higher cost.
Tip 4: Preventing Galvanic Corrosion in Systems Using 316 Stainless Fittings
Galvanic corrosion occurs when two different metals come into electrical contact in the presence of an electrolyte (e.g., water), causing accelerated corrosion of the more anodic metal.
How to Avoid Galvanic Corrosion
- Use fittings made of the same or compatible materials throughout the system.
- Apply non-conductive barriers or coatings between dissimilar metals.
- Ensure proper grounding and bonding of the piping system.
- Avoid using copper fittings or components in direct contact with 316 stainless steel.
Proper material selection and system design significantly reduce maintenance caused by galvanic corrosion.
Tip 5: Storage and Handling of 316 Stainless Fittings Before Use
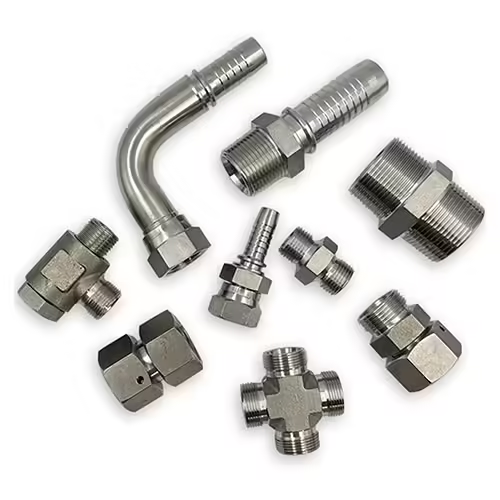
Even before installation, the way 316 stainless fittings are stored and handled can impact their long-term durability.
Best Practices
- Store fittings in a clean, dry environment away from direct contact with corrosive substances.
- Avoid stacking heavy items on fittings that can cause deformation or surface damage.
- Use protective packaging or coatings if storing for an extended period.
- Handle fittings with clean gloves to prevent contamination from oils or acids on hands.
Correct storage and handling help maintain the integrity of fittings, reducing early maintenance needs.
Conclusion
In summary, 316 stainless fittings offer exceptional advantages in corrosive and high-demand environments due to their chemical composition and physical properties. However, neglecting proper maintenance can compromise these benefits, leading to corrosion, leaks, and expensive repairs or replacements.
By following the five vital maintenance tips outlined—regular cleaning, diligent inspection, proper installation, galvanic corrosion prevention, and careful storage—industries can ensure the longevity and reliability of their 316 stainless fittings. This proactive approach minimizes downtime and maximizes the return on investment in these high-quality fittings.
FAQ
Q1: How often should I clean my 316 stainless fittings?
Cleaning frequency depends on the environment. For marine or chemical applications, every 1-2 weeks is recommended, while less harsh environments may only require monthly cleaning.
Q2: Can I use any type of lubricant on 316 stainless fittings?
Use lubricants and sealants that are compatible with stainless steel and the system’s fluid. Avoid petroleum-based lubricants if the system is food-grade or chemical-sensitive.
Q3: What are the signs that 316 stainless fittings need replacing?
Signs include visible corrosion or pitting, cracks, leaks, or fitting threads that have become loose or damaged.
Q4: Is it necessary to inspect fittings even if there are no leaks?
Yes, routine inspections help detect early signs of wear or corrosion before leaks or failures occur.
Q5: Can I mix 316 stainless fittings with other types of metal fittings?
It is generally not recommended due to the risk of galvanic corrosion unless proper insulating measures are applied.