Table of Contents
Why Choosing the Right Y Hose Connector Matters for Buyers
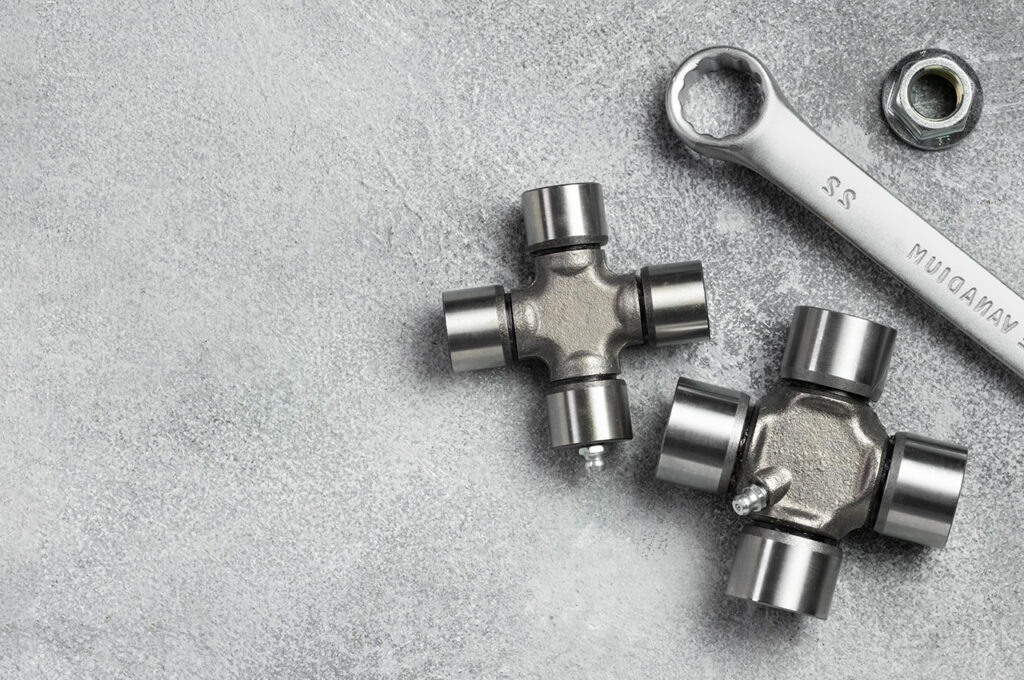
As a buyer, choosing the right y hose connector can feel overwhelming with so many options available. It’s common to face issues like leaks, poor fit, early wear, or missing features after purchase. These problems can cause wasted money, time-consuming repairs, or frequent replacements—frustrations no one wants.
A y hose connector may seem like a small component, but it plays a crucial role in splitting water flow efficiently and reliably. Whether you use it for home gardening, car washing, irrigation, or commercial applications, a good connector saves water, time, and energy while ensuring smooth operation.
This comprehensive guide is designed for buyers who want to make smart, informed decisions. We’ll cover the four essential tips you need to know before buying a y hose connector, including material choices, functional features, size compatibility, and application-specific advice. Read on to avoid common pitfalls and invest wisely.
1. Know Your Application: What Will You Use Your Y Hose Connector For?
Before you start comparing models, clearly define the intended use of your y hose connector. Different environments and tasks require different levels of durability and features.
Home Gardening & Light Use
If you’re watering a small garden or connecting hoses for occasional outdoor cleaning, you may get away with a plastic or zinc alloy connector. Look for:
- Lightweight design
- Budget-friendly price
- Moderate durability
Keep in mind, plastic connectors can degrade under UV exposure and may crack in cold weather.
Outdoor Heavy Use & Commercial Applications
For more demanding uses—such as large garden irrigation systems, greenhouses, or commercial car wash stations—durability is key. Opt for:
- Brass or stainless steel construction
- High corrosion resistance
- Robust design for frequent use
These materials withstand harsh weather, pressure fluctuations, and rough handling, extending product life.
Specialized Use Cases
Some buyers may need connectors for RV or marine plumbing, where saltwater corrosion is a concern, or for hot water lines that require heat-resistant components. Be sure to:
- Check temperature ratings
- Confirm corrosion-resistant alloys are used
- Consider certifications or industry standards compliance
Matching the y hose connector to your exact use ensures efficiency, longevity, and peace of mind.
2. Material Quality: Why It Makes or Breaks Your Purchase
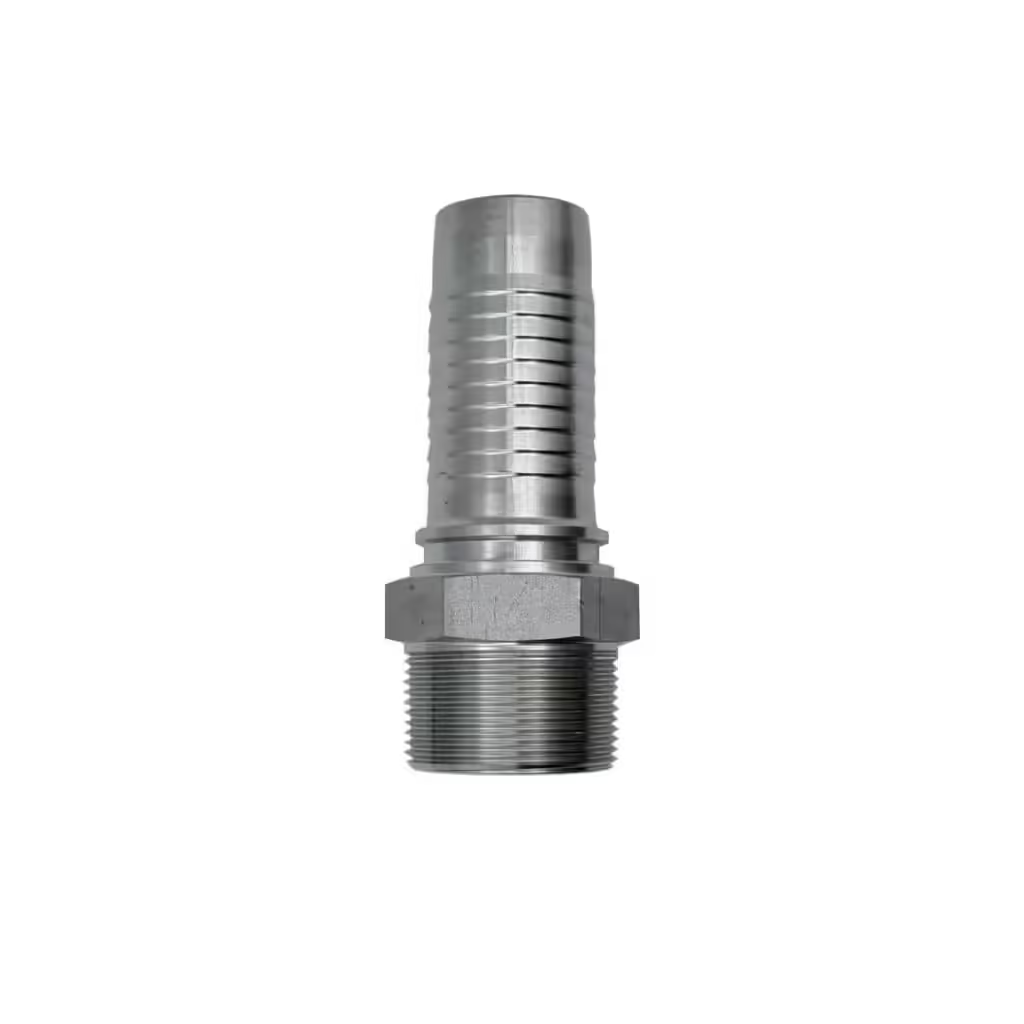
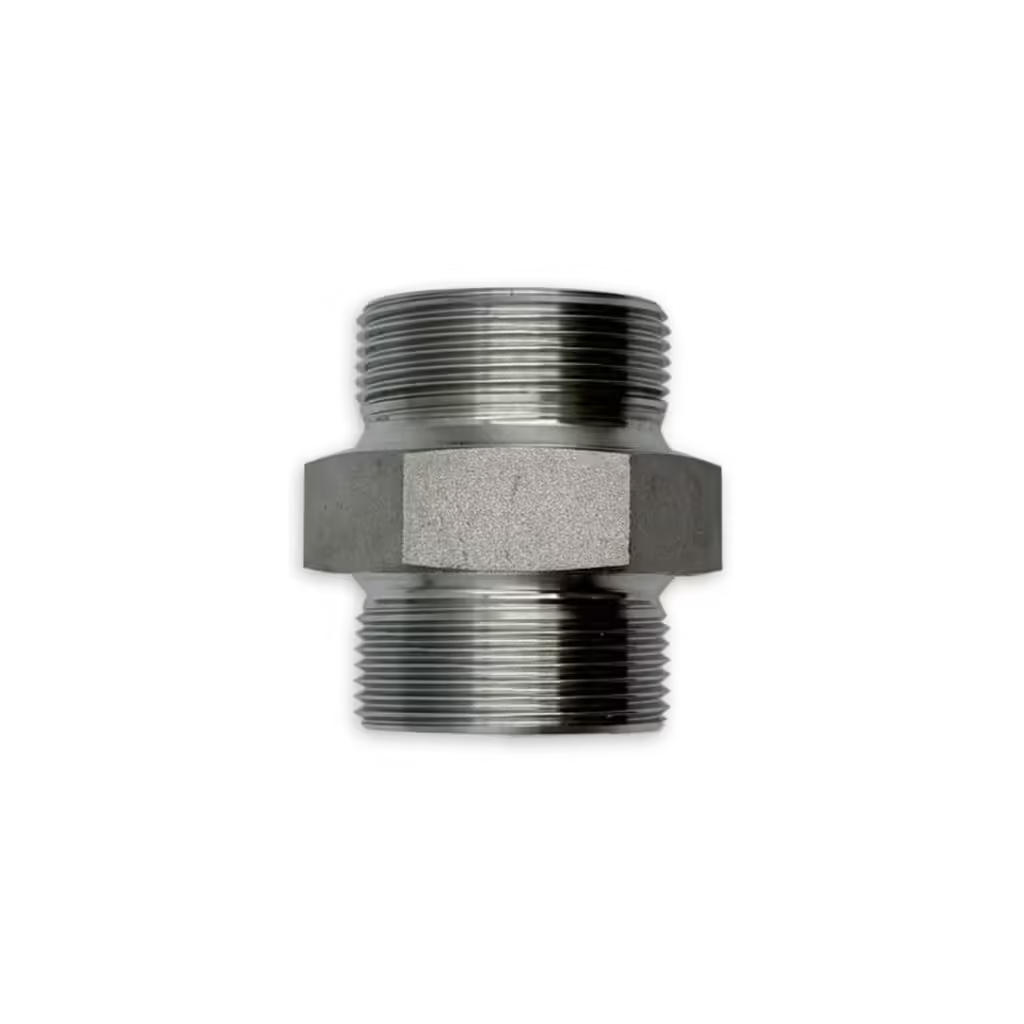
Material quality directly impacts how long your y hose connector lasts and how well it performs. Unfortunately, many low-cost options sacrifice durability for price, leading to leaks and failures within months.
Common Materials and Their Pros & Cons
Material | Durability | Corrosion Resistance | Typical Use Case | Cost |
---|---|---|---|---|
Brass | High | Excellent | Heavy-duty garden, industrial | Mid-High |
Stainless Steel | Very High | Excellent | Marine, harsh environments | High |
Zinc Alloy | Moderate | Good | Residential multi-season use | Medium |
Plastic (ABS, PVC) | Low to Moderate | Moderate to Low | Light residential, indoor use | Low |
Why Buy Metal?
- Resistance to UV and weather: Metals don’t degrade from sun exposure like plastics.
- Pressure tolerance: Brass and stainless steel handle high water pressures without cracking.
- Longevity: Expect several years of reliable use outdoors.
When Is Plastic OK?
- Indoor use or temporary outdoor tasks
- Occasional watering in mild climates
- Budget constraints—but expect shorter lifespan
Tips for Buyers:
- Ask for material certifications if available.
- Check user reviews focusing on durability and leak reports.
- Consider paying a bit more upfront for metal connectors—you save replacement hassle later.
3. Shut-Off Valves: Don’t Buy a Connector Without Them
One of the biggest annoyances buyers face is the lack of individual shut-off valves on y hose connectors. Without them, you must disconnect hoses completely to stop water flow, wasting time and risking damage.
Benefits of Shut-Off Valves
- Independent control: Turn water on/off separately for each hose without unplugging.
- Water saving: Quickly stop water flow to one outlet without affecting the other.
- Convenience: Makes multi-tasking easy (e.g., watering garden while washing car).
Valve Types to Look For
- Lever or knob-operated valves: Easy to turn even with wet hands.
- Smooth operation: Avoid stiff or flimsy valves that break or leak.
- Quality seals: Rubber or silicone washers prevent drips and leaks.
What Buyers Often Miss
- Some connectors have only one valve or none at all—check product descriptions carefully.
- Ergonomic designs can reduce hand fatigue during repeated use.
- Look for reinforced joints to avoid valve breakage under stress.
4. Size, Thread Type & Installation: The Most Overlooked Pitfall
Size incompatibility is the leading cause of wasted purchases. Many buyers don’t measure or confirm hose and spigot threads beforehand, resulting in leaky or unusable connectors.
Common Standards
- 3/4 inch Garden Hose Thread (GHT): Most standard in the US and many countries.
- Quick-connect fittings: Popular for rapid attach/detach but check compatibility.
- Swivel connectors: Prevent hose twisting and improve flexibility.
How to Avoid Mistakes
- Use a thread gauge or ruler to measure existing hoses and spigots precisely.
- Confirm the connector’s thread type matches your hoses—mixing metric and imperial threads causes leaks.
- If possible, buy connectors with swivel or rotating heads for easier handling.
Installation Tips
- Replace worn washers or O-rings during installation to ensure tight seals.
- Avoid overtightening to prevent thread damage.
- Test for leaks immediately after installation.
Bonus: Additional Features and Buyer Considerations
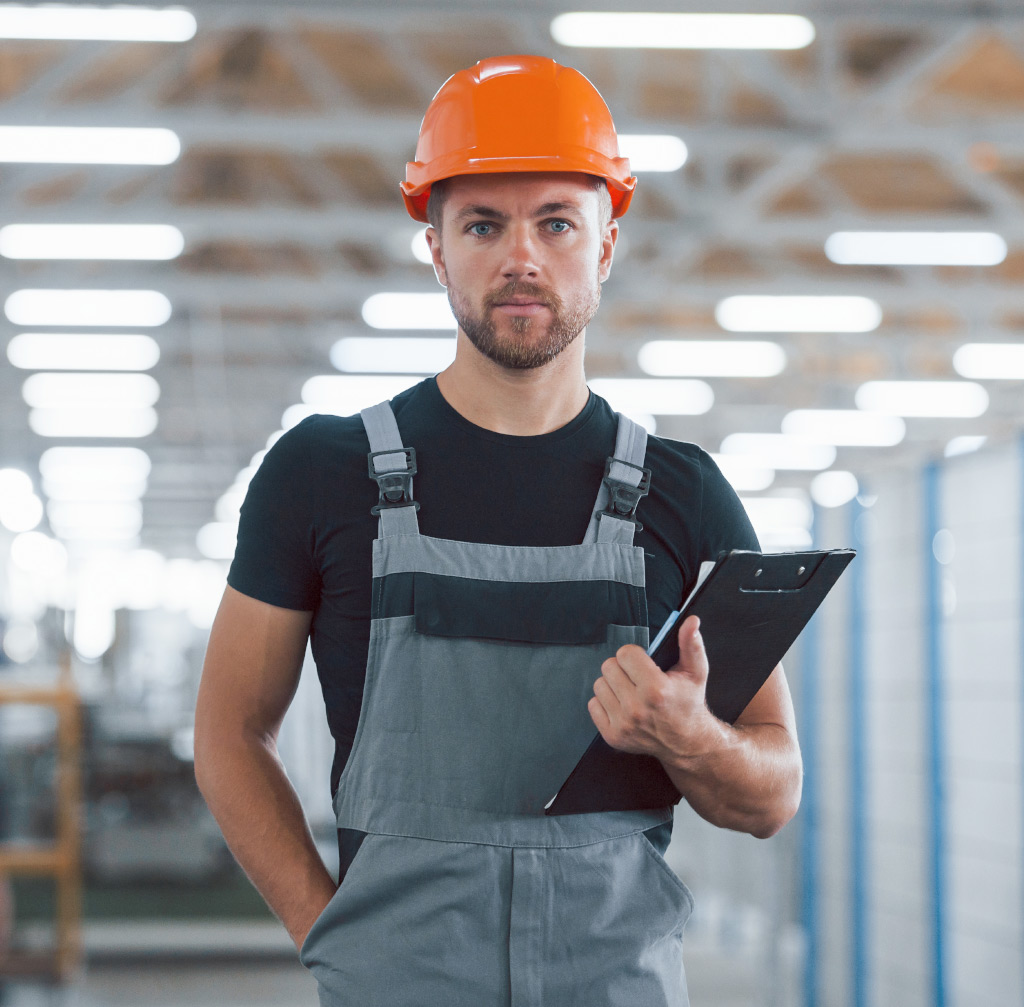
Anti-Leak Design
Look for connectors featuring enhanced sealing technology, such as double O-rings or pressure-tested joints, especially if you live in areas with hard water or fluctuating pressures.
Temperature Resistance
If your application involves warm or hot water (e.g., greenhouse irrigation), verify the temperature rating. Brass and stainless steel connectors usually handle up to 180°F (82°C), but plastics may deform.
Warranty & Support
Reputable sellers and manufacturers often back their connectors with warranties. Choose brands offering guarantees and responsive customer service to avoid headaches if issues arise.
Conclusion
Don’t let a small component like a y hose connector ruin your watering, cleaning, or industrial setup. By clearly understanding your application, prioritizing durable materials, insisting on shut-off valves, and confirming size compatibility, you can confidently buy a connector that lasts and performs flawlessly.
Remember, investing in a high-quality y hose connector pays off in reduced water waste, fewer replacements, and hassle-free daily use. Use this guide as your roadmap to smart purchasing and enjoy efficient, leak-free water distribution for years to come.
FAQ
Q1: Can I use any y hose connector for both indoor and outdoor use?
A: Not always. Choose plastic connectors for light indoor use and brass or stainless steel for outdoor or heavy-duty applications.
Q2: Are shut-off valves necessary?
A: Yes, they add essential control and convenience, especially if you regularly switch between multiple hoses.
Q3: What thread size do most y hose connectors have?
A: Most have 3/4 inch garden hose thread, but always measure your hoses to be sure.
Q4: How can I prevent leaks?
A: Proper size matching, good-quality washers, and tightening without overdoing it are key.
Q5: Can y hose connectors handle hot water?
A: Only those rated for temperature resistance, typically brass or stainless steel. Check product specs before use.