Table of Contents
Introduction
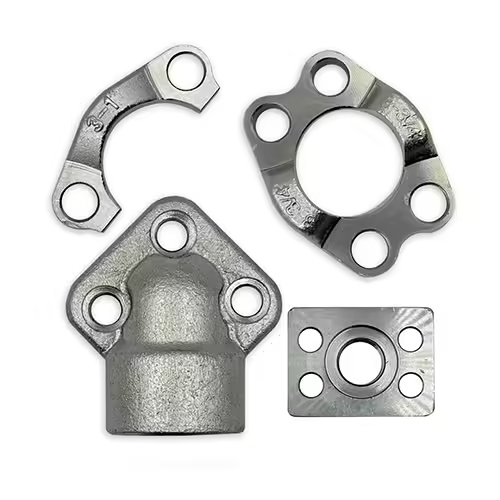
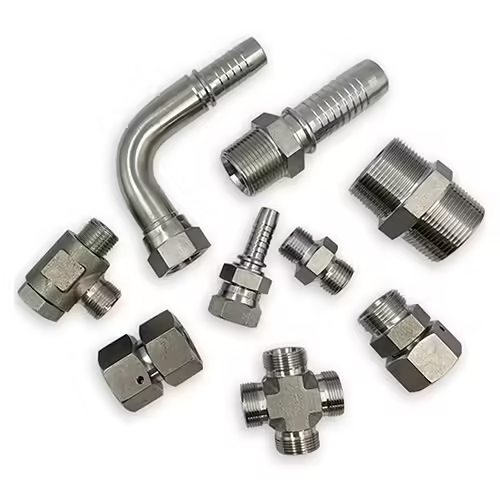
When it comes to fluid power systems, choosing the right components is crucial for performance, safety, and longevity. One of the most important elements in any hydraulic setup is the hydraulic compression fitting. These small but critical parts are designed to create a leak-proof connection between tubes and hoses in hydraulic systems, ensuring reliable fluid flow under high pressure. For buyers, especially those unfamiliar with industrial fittings, navigating the many options available on the market can be overwhelming. In this comprehensive guide, we’ll walk you through eight expert tips to help you confidently select the best hydraulic compression fitting for your needs.
From understanding material compatibility to identifying quality standards and installation techniques, these tips aim to equip you with everything necessary to make a well-informed purchase. Whether you’re outfitting a single machine or managing procurement for an entire operation, this blog will serve as your go-to resource.
Tip 1: Understand the Role of Hydraulic Compression Fitting
A hydraulic compression fitting connects tubes in a hydraulic system without the need for soldering or welding. It uses mechanical compression to create a tight seal that prevents leakage. These fittings are widely used in sectors such as construction, manufacturing, mining, and automotive due to their durability and ease of installation.
Understanding the role of these components helps buyers appreciate why quality and compatibility are so essential. Substandard fittings can lead to leaks, system failures, or safety hazards, all of which can be costly in industrial environments.
Tip 2: Choose the Right Material for Your Application
Hydraulic compression fitting materials must be selected based on the environment and fluid involved. The most common materials include:
- Brass: Corrosion-resistant, ideal for low to moderate pressure applications.
- Stainless Steel: Offers high strength and corrosion resistance, suitable for aggressive environments.
- Carbon Steel: Strong and cost-effective but requires plating to resist corrosion.
Each material offers different benefits and limitations. For example, brass is easy to install and resists corrosion but may not withstand very high pressure. Stainless steel, while more expensive, offers superior strength and is ideal for marine or chemical applications.
Tip 3: Consider Thread Type and Size
Choosing the correct thread type and size is essential for ensuring compatibility between the hydraulic compression fitting and other components in your system. Common thread types include:
- NPT (National Pipe Thread)
- BSPT (British Standard Pipe Tapered)
- JIC (Joint Industry Council)
- SAE (Society of Automotive Engineers)
Each thread standard serves specific regional and industrial purposes. Incorrect thread matching can lead to leaks or failure under pressure.
Use calipers and thread gauges to accurately identify the size and pitch of threads when replacing or purchasing fittings. Many reputable suppliers provide charts and tools to help with this.
Tip 4: Verify Pressure and Temperature Ratings
Hydraulic compression fittings are rated for specific pressure and temperature ranges. These ratings must align with the system’s operating conditions. Using a fitting with lower pressure capacity than required can lead to bursting or catastrophic failure.
Here’s a quick comparison table to help understand typical performance metrics:
Material | Max Pressure (PSI) | Temperature Range (F) | Corrosion Resistance |
---|---|---|---|
Brass | 3,000 | -65 to 250 | Moderate |
Stainless Steel | 6,000 | -425 to 1,200 | Excellent |
Carbon Steel | 5,000 | -20 to 400 | Low to Moderate |
Make sure to consider both static and surge pressures when selecting fittings. Overlooking peak conditions can be a critical mistake.
Tip 5: Evaluate Manufacturer Standards and Certifications
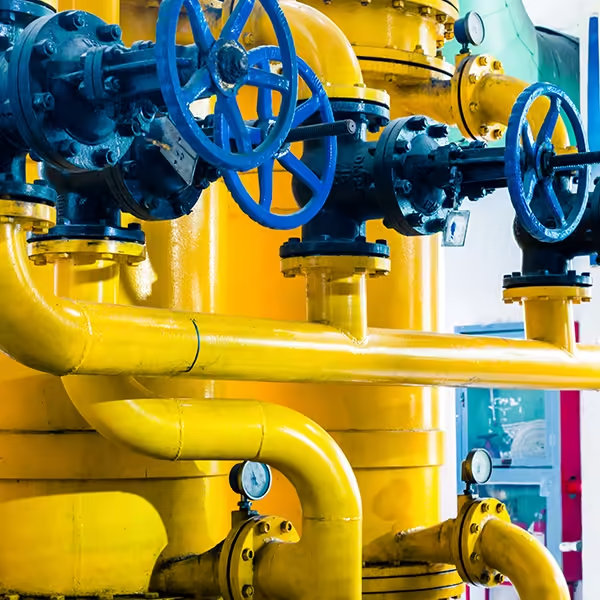
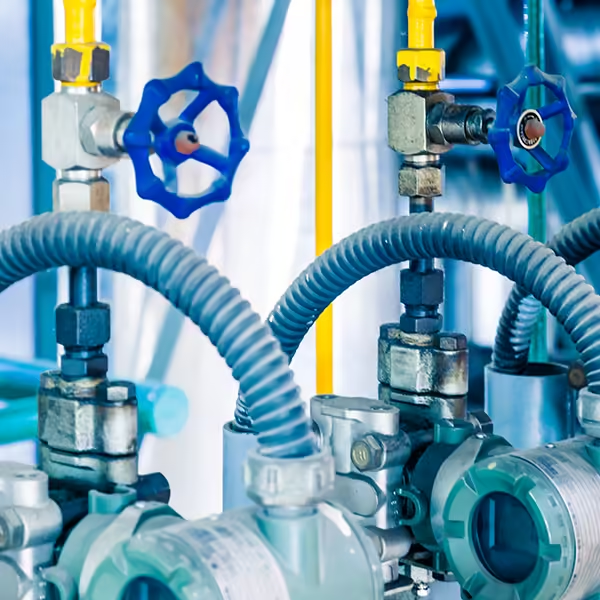
Not all hydraulic compression fittings are created equal. Reputable manufacturers adhere to strict quality assurance protocols and international standards. Look for fittings certified under:
- ISO 8434
- SAE J514
- DIN 2353
These standards guarantee consistency in dimensions, pressure ratings, and performance. Buying certified products also provides peace of mind regarding durability and safety.
Additionally, consider the manufacturer’s reputation, warranty, and customer support. Established brands are more likely to offer fittings that have undergone rigorous testing.
Tip 6: Assess Compatibility With Fluids and Lubricants
One of the most overlooked factors when selecting a hydraulic compression fitting is fluid compatibility. Hydraulic fluids differ not only in viscosity and thermal behavior but also in chemical reactivity with different metals and seal materials.
Common Hydraulic Fluids Include:
- Mineral Oil-Based Hydraulic Fluids: Most commonly used and generally compatible with steel, brass, and some polymers.
- Synthetic Fluids: These can include organophosphate esters, polyalphaolefins, or esters, which may react with certain rubber seals or softer metals.
- Water-Glycol Mixtures: Often used in fire-resistant applications but may corrode untreated steel or lead to premature aging of elastomer seals.
Steps to Ensure Compatibility:
- Use Material Compatibility Charts: Reputable suppliers often publish detailed chemical compatibility tables outlining which materials resist which fluid types.
- Consult OEM Recommendations: System manufacturers usually specify the preferred fittings or at least the material requirements.
- Avoid Trial-and-Error: Incorrect pairing can result in immediate leaks, internal corrosion, or even catastrophic failure of a hydraulic system.
Example: A buyer using phosphate ester fluid in an aviation ground-support vehicle opted for zinc-plated steel fittings. Within months, corrosion appeared around all joints. Switching to stainless steel with Viton® seals resolved the issue and prevented further system damage.
Tip 7: Installation Best Practices to Prevent Failures
Even the most expensive or high-performance hydraulic compression fitting can underperform—or fail entirely—if not installed properly. Improper installation remains one of the leading causes of leakage, cracking, and premature wear in hydraulic connections.
Installation Best Practices:
- Cleanliness Is Critical
Any dust, dirt, or metal shavings in the tubing or fitting body can compromise the seal or damage internal threads. Always clean all components thoroughly before assembly using lint-free cloths and approved solvents. - Use Proper Torque Settings
Over-tightening can distort threads or crush ferrules, while under-tightening may lead to weak seals or fitting blow-off under pressure. Always use a torque wrench calibrated to the manufacturer’s specifications. - Avoid Cross-Threading
Misalignment during threading can damage both the fitting and the tube, making the connection unsafe. Begin tightening by hand to ensure proper alignment before using tools. - Follow Manufacturer Instructions
Each type of hydraulic compression fitting may have unique installation steps. For example, two-piece and three-piece fittings require different ferrule seating techniques. Refer to datasheets or online installation videos provided by the manufacturer. - Perform Pressure Testing
After installation, pressurize the system gradually and check for leaks. Conduct tests under actual operating pressure, not just ambient or low-pressure tests, to ensure integrity.
Tip: Keep an installation log for large systems, noting who installed each section, with what torque setting, and on what date. This helps with future troubleshooting.
Tip 8: Budget Wisely Without Sacrificing Quality
Budget constraints are a reality for most buyers, whether you’re purchasing for a small workshop or managing procurement for a multi-site industrial operation. However, cost-cutting should never come at the expense of performance or safety when selecting hydraulic compression fittings.
Why the Cheapest Isn’t Always the Best:
Low-cost fittings often save on:
- Material purity (e.g., recycled metal alloys)
- Precision machining (leading to thread mismatch or burrs)
- Pressure testing or post-machining quality control
- Packaging and corrosion protection
A Better Way to Approach Budgeting:
Budget Factor | Cheap Fittings | High-Quality Fittings |
---|---|---|
Initial Price | Low | Moderate to High |
Lifespan | Short | Long |
Failure Rate | High | Low |
Downtime Risk | High | Low |
Long-Term Cost | High (due to replacements & downtime) | Low |
Recommendations:
- Focus on Lifecycle Cost: A slightly more expensive fitting with a 5-year life is cheaper over time than a low-cost fitting replaced every 12 months.
- Buy in Bulk: If your company uses large volumes, negotiate bulk discounts directly with manufacturers or authorized distributors.
- Evaluate Distributor Support: Choose distributors who provide logistics tracking, technical documentation, and flexible returns—not just low prices.
- Consider Supply Chain Stability: Especially important for international orders. A cheap part that’s out of stock for 8 weeks could halt production.
Example: One logistics company switched to ultra-low-cost fittings sourced from an unknown brand. After just six months, multiple systems began leaking, requiring emergency repairs and temporary shutdowns. Switching back to a trusted brand cut their annual repair cost by 42%.
Conclusion
Selecting the right hydraulic compression fitting requires a balance of technical understanding, practical evaluation, and informed decision-making. From material selection and pressure ratings to thread compatibility and certified manufacturing, every factor plays a crucial role in ensuring a safe and efficient hydraulic system.
By applying these eight expert tips, you’ll be better equipped to make confident purchasing decisions that lead to long-term system performance and reliability.
FAQ
Q1: What’s the main function of a hydraulic compression fitting?
It connects tubing in hydraulic systems using compression to create a leak-proof seal.
Q2: Can I reuse a hydraulic compression fitting?
Generally, these fittings are designed for one-time use, especially in high-pressure applications.
Q3: Are hydraulic compression fittings suitable for all types of fluids?
No, compatibility depends on the fluid and the fitting material. Always consult a compatibility chart.
Q4: What thread type should I choose for my application?
This depends on your system requirements and regional standards. NPT is common in North America, BSPT in Europe.
Q5: How can I identify a quality hydraulic compression fitting?
Look for certifications such as ISO or SAE, and buy from reputable manufacturers with strong quality control measures.
Q6: Is stainless steel always the best choice?
Not necessarily. While it offers excellent corrosion resistance, it may be overkill for low-pressure or non-corrosive environments.
Q7: Do all fittings need torque tools for installation?
Not all, but torque tools ensure consistent pressure and help prevent leaks or fitting damage.
Q8: How often should fittings be checked or replaced?
Routine inspections are recommended every few months, especially in high-pressure or critical systems.